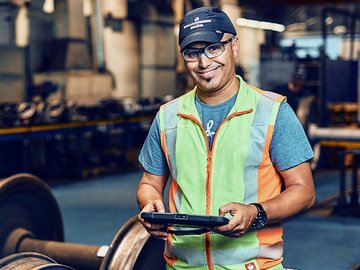
Company
Waggonwerk Brühl GmbH, a subsidiary of VTG, is synonymous with premium quality in freight wagon repair, maintenance and conversion since 1908.
History
In 1897, Deutsche Waggonleihanstalt – forerunner of what would later become Eisenbahnverkehrsmittel AG (EVA) – was founded in Berlin. As the wagon fleet grew, the young enterprise acquired a site in 1908 where it could carry out repairs and park rolling stock: the Waggonwerk was born. Halls and railway sidings were built on the premises. Investments also made it possible to build new, special-purpose rail freight wagons. In 1919, Deutsche Waggonleihanstalt moved off the site and into its own building at Kaiserallee 36/37 in Berlin.
The facility grew quickly and by 1930 was the largest and longest-standing privately owned repair workshop for rail freight cars in Germany. According to its own annual statistics, 3,000 special-purpose wagons were either built or serviced that year. Until 1942, the workshop also manufactured road vehicles, including superstructures and trailers for trucks. A wood-bending facility attached to the workshop and a woodworking shop took charge of making wagon-building products, which were sold via EVA. Company-owned homes for around 50 of its employees were erected nearby.
Starting in 2005, VTG and Waggonwerk Brühl massively ramped up their infrastructure. Among the biggest single investments were:
- Construction of the central VTG warehouse (2005)
- Construction of a new flare system to decompress gas tank cars (2006)
- Opening of a new wheelset workshop in compliance with VPI guidelines, modernisation of the water management system and renewal of the facilities for interior and exterior cleaning (2010)
- Construction of the wheelset warehouse (2013)
In the mid-2010s, Waggonwerk Brühl gradually expanded its geographical coverage by adding new service centers and workshops:
- Service center offering mobile maintenance opened in Oranienbaum (2014)
- Workshop offering stationary and mobile maintenance opened in Syke, near Bremen (2015)
- Workshop offering stationary and mobile maintenance opened in Schwarzheide (2016)
- Service center offering mobile maintenance opened in Hamburg; relocation of the Oranienbaum service center to Lutherstadt Wittenberg (2017)
- Service center offering mobile maintenance opened in Ahaus-Alstätte (2019)
- Service center offering mobile maintenance opened in Frechen, near Cologne (2020)
Company vision
Waggonwerk Brühl has been a successful company for over a century. One reason for our ongoing business success is the high quality of our services. Another is our corporate philosophy, which reflects our image of who we are as a company and what our mission is. Essentially, everything we do, every business decision we make is based on four key principles:
- Customer-centricity: We place the wishes, requirements and individual needs of our customers at the center of all our activities.
- Environmental awareness and conservation of resources: Fully aware of our responsibility toward the environment, we handle the resources at our disposal as sparingly as possible.
- Occupational health and safety for our staff: Our employees and their knowledge underpin our success. They are this company’s most valuable assets. Protecting their health and their jobs in line with the very latest standards is VTG’s top priority.
- Respectful and upright relations between management and employees: We willingly accept our responsibility and duty of care towards all employees. We see this company as one big team, working together to be successful. Everyone deserves the same respect and recognition – as colleagues and simply as human beings.
Innovations
Waggonwerk Brühl is always open to new ideas and makes use of innovative technology in the repair and maintenance of freight wagons. This approach gives both us and our customers an edge over our competitors. Why? Because innovation saves time and money. Just in the past few years, we have implemented the following innovations throughout our company:
- WIST software – Digitalisation of processes and documentation for wheelset reconditioning (2020)
- Digital, laser-based bogie measurement (2020)
- Digitalisation of the entire process chain (since 2021)
- Implementation of lean management methods across every link in the value chain (since 2022)